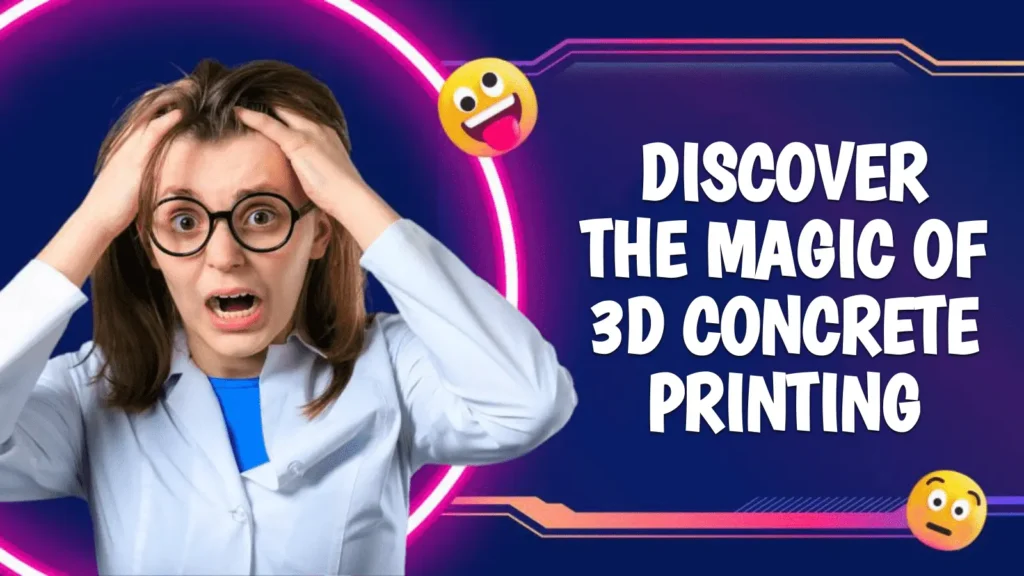
The innovation of concrete 3D printing has revolutionized the construction industry by offering enhanced efficiency, cost-effectiveness, and design flexibility in building structures. A concrete 3D printer enables construction projects to complete faster and with reduced labor costs.
Additionally, the ability to create complex and intricate designs using concrete 3D printing opens up new possibilities for architectural creativity. By leveraging the power of this emerging technology, construction companies can save on time and resources traditionally required for form work and manual labor.
Furthermore, the use of a concrete 3D printer allows for greater precision and accuracy in construction, minimizing errors and improving overall quality. The application of concrete 3D printing in the construction industry has the potential to disrupt traditional construction methods by offering numerous benefits. These include increased productivity, design flexibility, reduced construction time and costs.
3D printing concrete technology
3D printing concrete technology is an innovative construction method that utilizes additive manufacturing techniques to create structures layer by layer using a specially formulated concrete mixture. This technology allows for increased geometrical freedom and saves time, labor costs and enhances safety in the construction industry.
Large-scale 3D printing with concrete has been under development for the past decade and shows great potential in increasing productivity and design flexibility while reducing construction time and costs. By utilizing 3D printing technology, we can print concrete directly on-site, eliminating the need for traditional mold casting or structure building.
We specially prepare the concrete used in 3D printing to flow easily through the printing nozzle, allowing us to create intricate and complex shapes with ease.
Steps in 3d printing
3D printing is an innovative manufacturing process that allows the creation of three-dimensional objects from a digital design file.
The process of 3D printing typically involves three main steps:
- Pre-processing:In this step, specialized computer-aided design software creates a 3D model of the object. Then, the software slices the design into thin layers, which the 3D printer will use as a blueprint for printing.
- Printing: The sliced design file is sent to the 3D printer, which begins the printing process. The printer uses a variety of techniques and materials, such as filament or powder, to build the object layer by layer. Each layer is created by depositing the material in a specific pattern or shape, based on the instructions from the design file.
- Post-processing: Once you have printed the object, you may need to perform some additional steps to clean and finish it. These steps can include removing any support structures that you used during the printing process, sanding or polishing the surface, and potentially applying coatings or paint for a smooth and refined finish.
What type of concrete is used for 3D printing?
In 3D printing, people typically use a specialized type of concrete known as “3D printable concrete” or “concrete for additive manufacturing“. 3D printed concrete contributes to sustainability in construction by reducing material waste, labor costs, and construction time. Additionally, it allows for the optimization of material usage, reducing the overall environmental impact.
How does 3D printing concrete work?
3D printing concrete, also known as additive manufacturing with concrete, is an innovative construction technique. It involves the layer-by-layer deposition of specially formulated cement-based materials to create three-dimensional structures.
This process begins with a digital design model of the desired structure, which is then sliced into layers.
These layers are then fed into a 3D printer. The 3D printer uses an extrusion nozzle or another method to deposit the concrete material in precise patterns and shapes. As each layer is deposited, it bonds with the previous layers to gradually build up the structure.
What is 3D concrete made of?
3D concrete, also known as 3D-printed concrete or additive manufacturing of concrete, is a construction material that utilizes a combination of cementitious materials, aggregates (such as sand and gravel), water, and sometimes additives or admixtures.
These ingredients are carefully mixed together to create a paste-like consistency that can be extruded or deposited layer by layer using 3D printing technology.
The exact composition of 3D concrete may vary depending on the specific application and desired properties. But typically it consists of a blend of Portland cement, fine aggregates (such as sand), coarse aggregates (such as gravel or crushed stone), water, and other additives or admixtures.
What are the properties of 3D printed concrete materials?
The properties of 3D printed concrete materials are crucial in determining the quality and performance of the final structure. These properties include:
- Flowability: The ability of the concrete to flow smoothly through the printing nozzle, ensuring proper deposition and layering during the printing process.
- Viscosity: The resistance of the concrete to flow, which affects the printing speed and accuracy.
- Yield strength: The ability of the concrete to maintain its shape and support its own weight during the printing process, preventing deformation or collapse.
- Green strength: The initial strength of the printed concrete, which allows for the layering and building of subsequent layers without distortion or failure.
- Pumpability: The ability of the concrete to be pumped through nozzles, enabling smooth and continuous extrusion during the printing process.
- Interlayer bonding: The ability of the printed layers to adhere and bond together, ensuring structural integrity and preventing delamination or separation.
- Buildability: The resistance of the fresh concrete to deformation during construction and its ability to retain its extruded shape, enabling the formation of complex geometries and intricate designs without compromising structural stability.
What is the density of 3D printed concrete?
The density of 3D printed concrete plays a crucial role in determining its structural integrity and overall performance. The density of 3D printed concrete can vary depending on factors such as the composition of the mixture, printing parameters, and curing process.
How strong is the 3D printing of concrete houses?
3D printed concrete houses have emerged as a promising technology in the construction industry, offering potential benefits such as faster construction timelines and reduced material waste.
However, when considering the strength of 3D printed concrete houses, we need to take into account some factors.The strength of 3D printed concrete houses depends on various factors such as the quality of the materials used, design considerations, and the specific construction techniques employed.
It is essential to ensure that the concrete mixture used in 3D printing is of high quality and meets the necessary strength requirements.
3d concrete printing advantages and disadvantages
3D concrete printing, also known as additive manufacturing in construction, is a cutting-edge technology that offers numerous advantages and disadvantages.
Advantages
Some advantages of 3D concrete printing include:
- Faster construction: 3D concrete printing allows for the rapid production of structures, reducing construction time significantly compared to traditional methods.
- Reduced labor requirements:With 3D concrete printing, the automated process takes over most of the construction tasks, decreasing the need for manual labor.
- Increased design complexity and accuracy: 3D concrete printing enables architects and designers to create intricate and complex designs that would be challenging or even impossible to achieve with traditional construction methods.
- Waste minimization: 3D concrete printing is a precise process that only uses the necessary amount of material, minimizing waste and reducing environmental impact.
- Transportation savings: With 3D concrete printing, the construction team can print construction components directly on-site, eliminating the need to transport precast elements to the construction site and resulting in significant transportation savings.
Disadvantages:
Despite its advantages, 3D concrete printing also has some limitations and disadvantages. Disadvantages of 3D concrete printing include:
- Cost: The initial investment in 3D concrete printing technology can be high, making it less accessible for smaller construction companies or projects with limited budgets.
- Limited material options: Currently, traditional construction methods limit the range of materials that we can use in 3D concrete printing.
- Technical challenges: 3D concrete printing is a complex technology that requires skilled operators and technicians to ensure the proper functioning of the equipment and achieve high-quality results.
Strongest three-dimensional printer filament
When it comes to 3D printing, having a strong and reliable filament is crucial for creating durable and high-quality prints. One of the strongest three-dimensional printer filaments available on the market is carbon fiber filament. People know carbon fiber filament for its exceptional strength-to-weight ratio, which makes it ideal for applications that require structural integrity and durability.
Combining carbon fibers with a polymer resin creates this filament, resulting in a material that is lightweight yet incredibly strong. Industries such as aerospace, automotive, and sports equipment manufacturing commonly use it.
Carbon fiber filaments are able to withstand high temperatures and have excellent resistance to chemical corrosion. Additionally, carbon fiber filament is highly rigid and has low thermal expansion, allowing for precise and dimensionally accurate prints. Furthermore, the use of carbon fiber filament in 3D printing allows for the creation of parts with enhanced mechanical properties.
What is the strongest shape to 3D print?
When it comes to 3D printing, various factors affect the strength and durability of the printed object. However, studies have shown that certain shapes tend to provide stronger prints.
One of the strongest shapes to 3D print is the honeycomb or lattice structure. This structure consists of a network of interconnected hexagonal or triangular cells, which distribute the load evenly and efficiently. The outstanding mechanical properties of this honeycomb pattern, such as high strength-to-weight ratio and impact resistance, are well-known.
Furthermore, researchers have also found that TPMS structures are strong when 3D printed. These structures, which are based on the principles of triply periodic minimal surfaces, provide excellent mechanical properties. Manufacturers can use them as formwork and reinforcement in concrete beam applications.
Learn how camera captures an image
How can 3D printing revolutionize the manufacturing industry?
In recent years, 3D printing technology has emerged as a promising innovation in the manufacturing industry. The potential exists to revolutionize the way we design, prototype, and produce products. One of the major advantages of 3D printing is its ability to fabricate highly customized objects with complex geometries.
This is particularly valuable in industries where customization is a key requirement, such as aerospace, automotive, and biomedical sectors. In these industries, traditional manufacturing processes often involve complex and time-consuming methods, such as machining or molding. However, with 3D printing, the additive process allows for the creation of intricate and personalized designs directly from digital files. Additionally, 3D printing has the potential to significantly reduce fabrication time.
Use of 3d printers
3D printers use additive manufacturing technology to create three-dimensional objects by layering materials such as plastic, metal, or even food. The versatility of 3D printers allows for endless possibilities in various industries, ranging from manufacturing and engineering to healthcare. Even culinary arts benefit from the possibilities offered by 3D printers.
The ability to customize and prototype complex structures with 3D printing technology has become a game-changer in industries such as aerospace, electronics, medical and automotive.
The use of 3D printers has revolutionized the way we create and manufacture objects in various industries. Furthermore, 3D printers have also made a significant impact in the academic and scientific communities. Scientists and researchers are utilizing 3D printing technology to produce additively manufactured electrochemical sensors for analytical chemistry applications.
Is it expensive to print 3D?
When it comes to the cost of 3D printing, there are several factors that can contribute to the overall expenses involved in the process. These factors include the cost of the 3D printer itself, the materials used for printing, and any additional software or equipment needed. Additionally, the cost can also be affected by the complexity and size of the object being printed.
Furthermore, energy consumption is another important consideration when assessing the cost of 3D printing. There are ongoing expenses associated with running the printer, such as electricity and maintenance. Overall, the cost of 3D printing has decreased significantly over time. However, it is still important to carefully consider all these factors to accurately determine its affordability.